Herramientas manuales
La manipulación de herramientas manuales comunes como martillos, destornilladores, alicates, tenazas y llaves diversas, constituye una práctica habitual en talleres de mantenimiento. aunque a primera vista tales herramientas puedan parecer poco peligrosas, cuando se usan de forma inadecuada llegan a provocar lesiones (heridas y contusiones, principalmente) que de modo ocasional revisten cierta gravedad, hasta el punto de que un 7% del total de accidentes que se producen anualmente en España y un 4% de los calificados como graves, tienen su origen en la manipulación de una herramienta manual. Si bien las causas que provocan estos accidentes son muy diversas, pueden citarse como más significativas las siguientes:
- Calidad deficiente de las herramientas.
- Uso inadecuado para el trabajo que se realiza con ellas.
- Falta de experiencia en su manejo por parte del usuario.
- Mantenimiento inadecuado, así como transporte y emplazamiento incorrectos.
Recomendaciones generales
De acuerdo con estas consideraciones, las recomendaciones generales para el correcto uso de estas herramientas, con el fin de evitar los accidentes que pueden originar, son las siguientes:
- Conservación de las herramientas en buenas condiciones de uso.
- Utilización de las herramientas adecuadas a cada tipo de trabajo que se vaya a realizar.
- Entrenamiento apropiado de los usuarios en el manejo de estos elementos de trabajo.
- Transporte adecuado y seguro, protegiendo los filos y puntas y manteniéndolas ordenadas, limpias y en buen estado, en el lugar destinado a tal fin.
Recomendaciones específicas
A continuación se indican las recomendaciones a tener en cuenta, en el manejo de algunas herramientas manuales de uso más frecuente.
Máquinas portátiles
Las máquinas portátiles son aparatos mecánicos accionados por una fuente de energía (eléctrica, neumática o hidráulica) que generan en la herramienta un movimiento de rotación o de vaivén.
Las causas de los accidentes con este tipo de máquinas son muy similares a las indicadas para las herramientas manuales, es decir, deficiente calidad de la máquina; utilización inadecuada; falta de experiencia en el manejo, y mantenimiento insuficiente, si bien en las máquinas portátiles hay que añadir además, las que se derivan de la fuente de energía que las mueve. Conviene precisar también que los accidentes que se producen con este tipo de máquinas suelen ser más graves que los provocados por las herramientas manuales.
Los riesgos más frecuentes que originan las máquinas portátiles son los siguientes:
- Lesiones producidas por el útil de la herramienta, tanto por contacto directo, como por rotura de dicho elemento.
- Lesiones provocadas por la fuente de alimentación, es decir, las derivadas de contactos eléctricos, roturas o fugas de las conducciones de aire comprimido o del fluido hidráulico, escapes de fluidos a alta presión, etc.
- Lesiones originadas por la proyección de partículas a gran velocidad, especialmente las oculares.
- Alteraciones de la función auditiva, como consecuencia del ruido que generan.
- Lesiones osteoarticulares derivadas de las vibraciones que producen.
Por el tipo de movimiento de la herramienta, las máquinas portátiles pueden clasificarse en dos grupos:
- De herramienta rotativa. En estas máquinas, la fuente de alimentación imprime a la herramienta un movimiento circular.
- De percusión. La fuente de energía imprime a la herramienta en este tipo de máquinas un movimiento de vaivén.
Máquinas portátiles de herramienta rotativa
Dentro de las máquinas portátiles, las de herramienta rotativa son las más frecuentes, destacando las siguientes: amoladoras o radiales, sierras circulares y taladradoras, cuya descripción se aborda seguidamente, considerando los riesgos más característicos y su prevención.
Máquinas portátiles de percusión
Entre las máquinas portátiles de percusión, una de las más comunes es el martillo neumático (figura 4) en sus más variadas versiones, utilizado en gran número de trabajos, adaptando en cada caso la herramienta más adecuada.
Figura 4
Los principales riesgos que se derivan del manejo de esta herramienta son los siguientes:
- Lesiones osteoarticulares provocadas por las vibraciones debidas al efecto de retroceso.
- Proyecciones de esquirlas y cascotes del material sobre el que se trabaja.
- Rechazo y proyección del útil que se está empleando.
- Hipoacusia a causa del ruido que se genera.
En lo que concierne a la prevención de estos riesgos cabe señalar que algunos fabricantes han logrado desarrollar sistemas percutores que minimizan el efecto de retroceso, reduciendo a su vez el nivel de ruido y el peso de la herramienta.
En cuanto al rechazo y proyección del útil puede evitarse mediante dispositivos de retención emplazados en el extremo del cilindro del martillo.
Debe vigilarse con frecuencia el buen estado de dichos dispositivos, porque en caso de rotura pueden proyectarse fragmentos de metal sobre las personas que se encuentran en las inmediaciones.
Ante el riesgo de proyección de fragmentos del material sobre el que se acciona el martillo neumático, deben disponerse pantallas que protejan a las personas y puestos de trabajo del entorno.
Los usuarios de este tipo de herramientas deben ir provistos de casco, guantes, gafas de seguridad y protección auditiva.
Máquinas herramientas destinadas al mecanizado de metales
Las máquinas herramientas son máquinas no portátiles accionadas con motor y destinadas al mecanizado de metales.
Todas las máquinas y equipos de trabajo nuevos deberán disponer de marcado CE, así como de declaración CE de conformidad. Este requisito es aplicable siempre:
- A todas las máquinas nuevas, aunque no presenten riesgo algunopara la seguridad de los usuarios
- A todas aquellas que sean de fabricación propia, aunque no se comercialicen
- En aquellos casos en que se monten máquinas o partes de máquinas de orígenes diferentes
El requisito anterior no será de aplicación, cuando se acople a una máquina o a un tractor un equipo intercambiable.
La declaración CE de conformidad acredita que la máquina o equipo de trabajo cumple los requisitos esenciales de seguridad y su firma posibilita la colocación de la marca CE en la máquina o equipo en cuestión.
En cuanto a los equipos y máquinas fabricadas antes del 1 de enero de 1995 que no dispongan de marcado CE, deben ponerse en conformidad con arreglo a lo establecido en el Real Decreto 1215/1997, de 18 de julio.
Una forma de abordar la problemática legal que generan las máquinas y equipos de trabajo es realizar un inventario que permita conocer con exactitud las carencias existentes.
Se entiende por mecanizado, el conjunto de operaciones de conformación en frío con arranque de viruta, mediante las cuales se modifican la forma y dimensiones de una pieza metálica. Las máquinas herramientas imprimen a la herramienta y a la pieza objeto de conformación, los movimientos precisos, para que se alcance la forma y dimensiones requeridas. Entre tales máquinas destacan algunas como: tornos, taladradoras, mandrinadoras, fresadoras, brochadoras, rectificadoras y otras que realizan operaciones derivadas de las anteriormente citadas.Aunque no desarrollan operaciones de mecanizado propiamente dichas, también se consideran máquinas herramientas las sierras mecánicas.
A continuación, se describen las disposiciones mínimas generales de seguridad recogidas en el Real Decreto 1215/1997, de 18 de julio, ya mencionado, que deben reunir las máquinas herramientas, cuyo cumplimiento contribuye a prevenir los riesgos más frecuentes que se derivan de la manipulación de estos equipos y que básicamente son:
- Contacto accidental con la herramienta o la pieza en movimiento
- Atrapamiento con los órganos de movimiento de la máquina
- Proyección de la pieza o de la herramienta
- Dermatitis por contacto con los fluidos de corte utilizados como refrigerantes.
Órganos de accionamiento:
Los órganos de servicio de estas máquinas deben ser claramente visibles e identificables y en caso necesario, llevar el etiquetado apropiado. Los colores indicativos de dichos órganos son:
- Puesta en marcha o en tensión: BLANCO.
- Parada o puesta fuera de tensión: NEGRO.
- Parada de emergencia: ROJO.
- Supresión de condiciones anormales: AMARILLO.
- Rearme: AZUL.
Los órganos de mando pueden ser de los siguientes tipos:
- Pulsador: Salvo el de parada deben estar encastrados.
- Pedal: Protegido contra accionamientos involuntarios.
- Barra paralela: Según la normativa vigente no debe utilizarse.
- Mando a dos manos: Será de tipo pulsador. Debe tener sincronismo y ser eficaz contra el burlado.
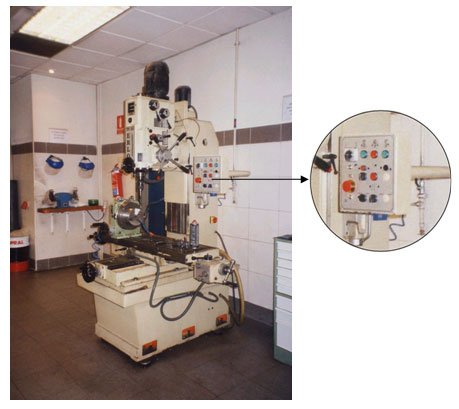
Figura 5: Taladro vertical. Órganos de Accionamiento
Estarán situados en la proximidad del puesto de mando y fuera de la zona de peligro, salvo el de parada de emergencia. Asimismo, desde el puesto de mando se dominará toda la zona de operación. En caso contrario, la puesta en marcha será precedida de alguna señal de advertencia acústica o visual.
Puesta en marcha
Debe obedecer a una acción voluntaria del operador sobre un órgano de accionamiento puesto a tal fin.
Tras un corte de energía (eléctrica, neumática, hidráulica), su posterior reanudación no deberá dar lugar a la puesta en marcha de las partes peligrosas de la máquina.
Se debe impedir que una máquina herramienta se ponga en marcha:
- Por el cierre de un resguardo con dispositivo de enclavamiento.
- Cuando una persona se retira de una zona cubierta por un dispositivo sensible, tal como una barrera inmaterial.
- Por la maniobra de un selector de modo de funcionamiento.
- Por el desbloqueo de un pulsador de parada de emergencia.
- Por el rearme de un dispositivo de protección térmico.
Parada
La orden de parada debe tener prioridad sobre todas las demás. Se consideran los siguientes tipos de paradas:
- Parada general: Toda máquina herramienta debe tener una parada de categoría 0, es decir, supresión inmediata de la energía de los accionadores de la máquina.
- Parada desde el puesto de trabajo: Está destinada a permitir que un operador pueda parar la máquina cuando tenga que intervenir en una zona peligrosa para una operación concreta. A su vez, este tipo de parada puede ser:
- De categoría 1, de modo que al ordenar la función de parada ésta se produce cuando la máquina se halla en posición de seguridad
- De categoría 2, de manera que al ordenar la función de parada la máquina se detiene en ese momento, pero mantiene sus fuentes de energía activadas.
- Parada de emergencia: Accionada por un dispositivo que debe permitir la parada de la máquina en las mejores condiciones posibles, mediante una deceleración óptima de los elementos móviles. Esta parada puede ser de categoría 0 o de categoría 1.
El órgano de mando que permite obtener esta función de parada de emergencia (pulsador de manotazo, cable, barra, etc.) debe ser de color rojo y estar colocado sobre fondo amarillo. La colocación de un dispositivo de parada de emergencia sólo tiene sentido en el caso de que el tiempo de parada que permite obtener sea netamente más corto que el obtenido con la parada normal, lo que requiere un frenado eficaz.
Caídas y proyecciones de objetos
Debe prevenirse la proyección de viruta y las salpicaduras de fluidos de corte, así como la posible caída de objetos, debidos tanto al funcionamiento propio de la máquina como a circunstancias accidentales.Las medidas preventivas a adoptar están destinadas a proteger no sólo a los operadores, sino también a cualquier otra persona que pueda estar expuesta a estos peligros. Consisten esencialmente en resguardos fijos o móviles de resistencia adecuada.
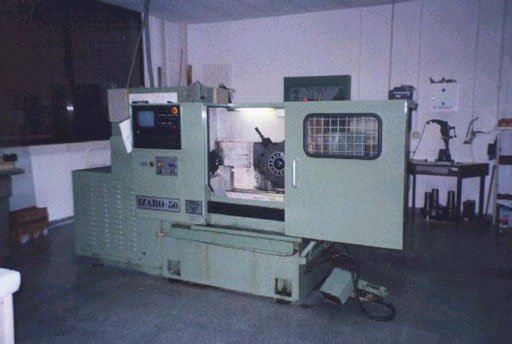
Figura 6. Fresadora de control numérico provista de resguardo móvil
Emisión de gases, vapores, líquidos y polvos
Cuando en una máquina herramienta pueda existir riesgo de emisión de algunos de estos elementos (por ejemplo, nieblas de fluidos de corte), se procurará efectuar su captación en su propio origen mediante un dispositivo de extracción localizada, integrado en lo posible en los resguardos o carcasas. Se estudiará en cada caso particular el tipo de emisión producida y se diseñará el elemento extractor en función de sus características.
Mantenimiento
- Se respetarán las condiciones de utilización de estas máquinas, tal como se recomienda por los fabricantes.
- Se prestará un atento cuidado al mantenimiento, especialmente cuando no sea posible colocar protectores eficaces y se realizará un correcto reglaje.
- La limpieza y reparaciones se llevarán a cabo con la máquina parada. En cuanto a las reparaciones en concreto, solamente las realizará personal especializado y debidamente autorizado.
Elementos móviles
Se distinguen en general, dos tipos de elementos móviles:
- Elementos móviles de transmisión: Se encuadran en este grupo los árboles de transmisión, poleas y correas.
- Elementos móviles de trabajo: Son aquellos que ejercen una acción directa sobre el material y desarrollan su actuación en la zona de operación, como la hoja de la sierra de cinta mecánica que se muestra en la figura 7.
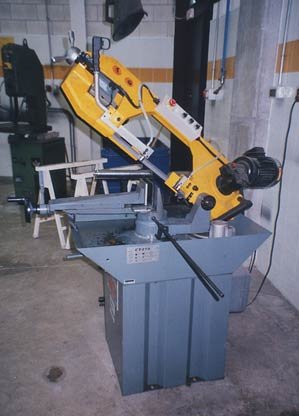
Figura 7. Sierra de cinta mecánica para corte de metales
Separación de las fuentes de energía
En lo referente a la energía eléctrica, la separación puede quedar asegurada mediante:
- Un interruptor-seccionador.
- Un disyuntor que disponga de la función de seccionado.
- Una toma de corriente para una intensidad inferior o igual a 16 amperios y una potencia total inferior a 3 KW.
Los dispositivos de separación deben ofrecer todas las garantías de que a cada posición (abierto/cerrado) del órgano de mando corresponda de forma inmutable la posición (abierto/cerrado) de los contactos.
Señalización y advertencia
En aquellas máquinas que tras adaptarle medidas de protección adecuadas persista un riesgo residual, éste deberá estar adecuadamente señalizado mediante indicadores normalizados.
Puesta en obra
La máquina estará ubicada en lugar nivelado y firme, evitando los lugares que puedan generar riesgos de caídas de altura. Asimismo, la zona de ubicación estará limpia, seca y ventilada.
Dispondrá de un servicio eléctrico encabezado por un diferencial adecuado con su correspondiente interruptor magnetotérmico y petaca de conexión tipo estanca, de conformidad con lo establecido en el Reglamento Electrotécnico de Baja Tensión.
Utilización
El personal que manipule este tipo de máquinas contará con la debida autorización y formación específica.
La máquina se fijará de manera que no se produzcan movimientos no deseables originados por vibraciones.
Antes de poner en marcha una máquina, se comprobará que no hay nadie manipulándola.
Otras consideraciones
Cualquier máquina herramienta deberá llevar su marcado CE correspondiente. Si su adquisición ha sido anterior a 1995 y carece de dicho marcado, se procederá a su puesta en conformidad, según lo establecido en el Real Decreto 1215/1997, de 18 de julio, como oportunamente se indicó.
Toda máquina dispondrá del correspondiente manual de instrucciones y libro de mantenimiento y revisiones en castellano facilitado por el fabricante.
Precauciones a tener en cuenta en la manipulación de fluidos de corte
Se considera que más del 98% de la energía mecánica que entra en juego en una operación de mecanizado se transforma en calor, en función de variables tales como el tipo de material, ángulo y profundidad de corte y velocidad del mecanizado. Con el fin de evitar un sobrecalentamiento en el punto de corte, que conduciría inevitablemente a un deterioro prematuro de la herramienta y a un acabado superficial indeseable de la pieza, el calor producido en la operación debe ser eliminado del modo más rápido y eficaz posible, para lo cual se utilizan los llamados fluidos de corte, que pueden definirse como líquidos de composición variada, que se adicionan al sistema pieza-herramienta-viruta de una operación de mecanizado, con el fin de lubricarlo y eliminar el calor que se genera (figura 8).
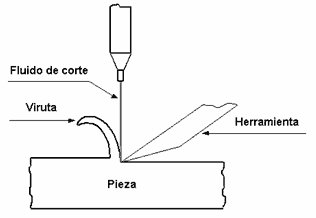
Figura 8. Adición de un fluido de corte a una operación de
mecanizado de una pieza metálica.
Atendiendo a su contenido en aceite mineral, los fluidos de corte pueden clasificarse en:
- Fluidos aceitosos o aceites de corte propiamente dichos.
- Fluidos acuosos, conocidos en España coloquialmente con el nombre de taladrinas.
A su vez, estas últimas se dividen en:
- Emulsiones simples.
- Sintéticas.
- Semisintéticas.
- Neosintéticas.
Todos estos fluidos de corte, cuyas funciones esenciales durante el mecanizado son refrigerar y lubricar, suelen contener un variado surtido de aditivos que les confieren propiedades tales como, estabilizar las emulsiones; inhibir la corrosión de piezas, herramientas y equipos de trabajo; reducir la proliferación de microorganismos (bacterias, hongos y levaduras); evitar la formación de espumas; disminuir o aumentar la dureza del agua, etc., con lo que a la propia agresividad de los productos de base, hay que añadir la que proporcionan los citados aditivos.
Las medidas preventivas frente a las afecciones cutáneas deberán orientarse hacia la consecución de dos objetivos concretos:
- Evitar la aparición de cualquier caso de dermatosis.
- Tratar eficazmente los casos que puedan aparecer, a fin de impedir su evolución.
La estrategia a desarrollar comprende cuatro líneas de actuación:
- Extremar la higiene personal y la limpieza del entorno de trabajo.
- Conocer los componentes de los productos utilizados, a través de la fichas de seguridad.
- Desarrollar un programa de protección dermatológica que incluya el uso de cremas barrera o guantes de protección, cuando sea posible, en el transcurso del trabajo; jabón neutro para el aseo personal antes de comer y al finalizar la jornada, y crema hidratante para restituir el manto ácido de la piel al finalizar el trabajo.
- Vigilancia médica permanente, estableciendo un registro de dermatosis.
|